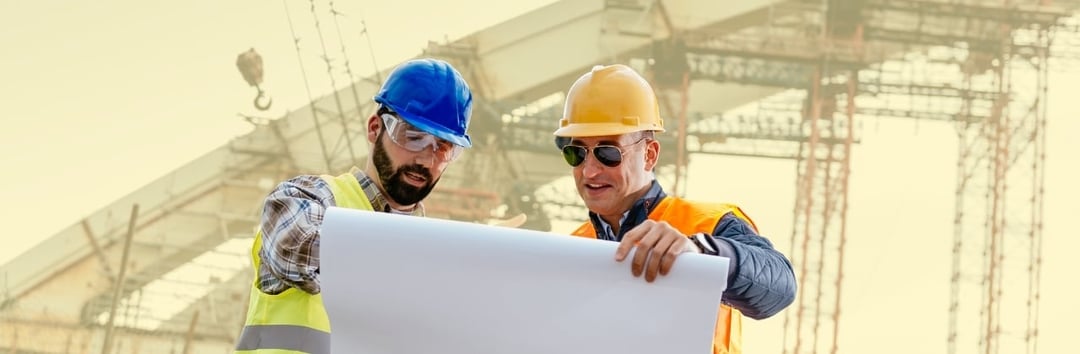
What is Takeoff in Construction?
Enhancing project planning with construction takeoffs
Construction takeoff is a fundamental cornerstone of project planning and management. Takeoff refers to the detailed process of itemizing materials from architectural drawings or blueprints, serving as a bridge between conceptual design and practical implementation. This process, which can be also referred to as quantity takeoff, helps to ensure precision in every aspect of project preparation, from budgeting to procurement.
Understanding what is a takeoff in construction is essential for anyone in the industry. In the current construction landscape, where margins are narrow and material costs are on the rise, the importance of accurately estimating the costs of a project cannot be overstated.
Construction professionals must make precise projects and optimize their bids to stay competitive and profitable. Construction takeoffs are instrumental in this regard, ensuring that each material and resource is carefully accounted for. This minimizes waste and optimizes resource allocation, thereby protecting the project’s budget, boosting operational efficiency, and increasing client satisfaction.
To shed light on the takeoff process, we’ve put together a detailed guide that provides valuable insights and best practices. Our goal is to equip you with the knowledge and tools to refine your project planning processes, ensuring efficiency and effectiveness in your construction projects.
Understanding what is a takeoff in construction
At the outset of any construction project, one of the initial steps before the first shovel hits the ground is the takeoff process. As explained by Guilianna M. Lozano of California Polytechnic State University, this process, often called quantity takeoff, encompasses a detailed review of available architectural drawings or blueprints. During this phase, estimators carefully measure and count the materials that the architect or engineer requires to construct the project.
The financial stakes in construction are high, with significant impacts on both builders and clients. Any uncertainty surrounding the final cost of a project, regardless of its size, poses a significant challenge. As such, the preconstruction phase demands ample time and effort to precisely estimate the total cost of the project. This is where takeoffs become indispensable.
Particularly in heavy, large-scale infrastructure projects like roads, bridges, and utilities, which cover extensive areas and use a wide array of materials and components, the precision of the takeoff is paramount. Employing a meticulous approach aids in effective resource allocation, maintaining budget control, and ensuring overall project success.
Construction takeoffs vs. construction estimates
In construction project management, the terms takeoff and estimate are similar yet different. Having already covered the concept of construction takeoff, we’ll now cover how an estimate diverges and offers a more comprehensive financial analysis.
While a construction takeoff zeroes in on quantifying materials required for a project, an estimate extends this scope to include a complete financial overview. An estimate incorporates the detailed material quantities derived from the takeoff with labor costs, equipment expenses, indirect costs such as permits and insurance, and often, a contingency for unexpected expenses.
The key distinction between construction takeoffs and estimates is their scope and detail. Takeoffs lay the groundwork by detailing material needs, whereas estimates use this information as a base to build a detailed financial model of the entire project. This includes all associated costs, offering stakeholders a transparent view of the project’s financial health and its potential return on investment.
If you’re interested in exploring more about the differences between construction takeoffs and construction estimates, our blog on construction estimating software vs. construction takeoff software provides further insights, elaborating on how these tools can be effectively utilized together to enhance project planning and execution.
Unpacking the takeoff process
The takeoff process is an important preliminary phase of any construction project, setting the stage for accurate project planning and execution.
This section will walk you through the steps involved in performing a construction takeoff, highlighting the components that are typically included.
Examination of project plans
Initiating a takeoff begins with a thorough examination of the project plans or blueprints. This review is not a simple look over the plans but a detailed analysis that seeks to understand every aspect of the design, from the core structural elements to the smallest finishing details.
Material quantity calculations
Once the project plans are fully reviewed, the next step is to calculate the quantities of materials needed. This involves measuring dimensions, areas, and volumes directly from the blueprints.
Consider a highway expansion project. The takeoff process would involve calculating vast quantities of asphalt for paving, concrete for bridges and overpasses, and steel for reinforcement. The complexity and scale of heavy construction projects like this necessitate an elevated level of precision in the takeoff process.
Consideration of labor and ancillary costs
While takeoffs traditionally focus on material quantities, a more holistic approach also considers the labor associated with each component and ancillary expenses like transportation and storage. This broader perspective can provide a more accurate reflection of the total material and labor costs, although it may blend the lines between a pure takeoff and a preliminary estimate.
Compilation and review
The final step involves compiling all the gathered information into a comprehensive document. This document should clearly list all materials, quantities, and associated labor (if included), organized in a manner that aligns with the project’s execution plan. A thorough review of this compilation is essential to ensure accuracy and completeness, providing a solid foundation for the subsequent estimating phase.
The evolution of manual to digital takeoffs
The process of conducting construction takeoffs can be approached in two distinct ways: the traditional manual method and the more contemporary digital method, which is facilitated by advanced construction takeoff software.
Manual takeoffs
Manual takeoffs are performed with physical blueprints, a scale ruler, a calculator, and meticulous attention to detail. This method involves:
- Blueprint analysis: The construction estimator begins by thoroughly reviewing physical blueprints, pinpointing every material the project demands.
- Measurement and calculation: Using a scale ruler, the estimator measures dimensions and calculates quantities directly from these plans. This step requires a high level of accuracy to avoid costly errors.
- Material listing: All identified materials and their corresponding quantities are listed manually, often categorized by type or project phase for clarity.
- Labor estimation: If labor considerations are included, estimators manually gauge the time required for each task based on experience and industry standards.
Manual takeoffs are characterized by their reliance on human expertise and the tactile experience of engaging with physical plans. However, this method is time-consuming and prone to human error, particularly in complex projects.
Digital Takeoffs
Digital takeoffs use specialized software to streamline and enhance the accuracy of the takeoff process. Key steps include:
- Digital plan import: Project blueprints are uploaded into takeoff software, allowing for an interactive review process.
- On-screen measurements: The software enables estimators to make precise measurements directly on digital plans, often with functionalities that automate calculations for areas, volumes, and more.
- Automated quantity extraction: Advanced software can automatically identify and quantify materials based on the specifications within the digital plans, drastically reducing manual input and the potential for error.
- Integrated labor and cost analysis: Many digital takeoff tools also offer features to estimate labor and material costs, providing a more thorough project overview.
Digital takeoffs provide increased efficiency and precision, especially for large or complex projects. The ability to save and adjust digital plans on the fly further adds to the flexibility and scalability of this method.
Choosing between manual and digital takeoffs
The choice between manual and digital takeoffs often depends on the project's scale, complexity, and the resources available. For small-scale projects or those with limited budgets, manual takeoffs might be the preferred route due to their lower costs. In contrast, larger or more complex projects can significantly benefit through the use of digital takeoff software due to its efficiency, accuracy, and integrated project management features.
The shift toward construction takeoff software is becoming the standard in the industry. In fact, in a survey conducted by Guilianna M. Lozano of California Polytechnic State University of nearly 60 construction firms, 83% responded that they had been using construction takeoff software for more than four years. driven by the continuous advancement of technology and an increasing demand for swift, accurate project planning and execution.
By understanding the nuances of both manual and digital takeoffs, construction professionals are equipped to make well-informed decisions that best suit their project needs. This strategic decision-making ensures that material estimation is executed accurately and efficiently, laying the groundwork for the successful completion of the project.
The impact of accurate takeoffs in project success
The precision of takeoffs in construction planning can directly influence the overall success of a project. Accurate takeoffs ensure that all aspects of a construction project, from budgeting to execution, are based on reliable data, leading to numerous benefits and mitigating risks associated with inaccuracies.
Direct benefits of accurate takeoffs
- Cost savings: One of the most significant advantages of accurate takeoffs is the potential for substantial cost savings. Accurately quantifying the materials required for a project can help prevent over-purchasing, thereby reducing waste and ensuring that funds are used effectively.
- Optimized resource allocation: Accurate takeoffs allow project managers to better allocate resources, allowing for materials, labor, and equipment to be efficiently utilized throughout the project lifecycle.
- Improved bid competitiveness: In the competitive construction bidding environment, accuracy in takeoffs can be a differentiator. Firms that can provide accurate estimates are more likely to win contacts because their bids reflect a realistic and trustworthy assessment of project costs.
Consequences of inaccurate takeoffs
On the other hand, inaccuracies in takeoffs can lead to a range of challenges that are particularly detrimental to large-scale, heavy construction projects.
- Project delays: Inaccurate takeoffs can result in material shortages, causing delays as additional materials are ordered and delivered. For infrastructure projects that often have tight schedules, these delays can disrupt the project timeline while also impacting public use and convenience.
- Budget overruns: Underestimating material needs can lead to unexpected extra expenses, pushing projects over budget. In heavy construction, where projects are typically high-value, budget overruns can be significant and impact financial viability.
- Reputational damage: Consistently inaccurate takeoffs can harm a construction firm’s reputation, making it difficult to secure future work. Maintaining a reputation for reliability and accuracy is particularly crucial in high-profile projects that are closely monitored by stakeholders and the public.
Enhancing takeoff accuracy with advanced strategies
Improving the accuracy and efficiency of construction takeoffs can lead to your firm achieving more success.
Several strategies, as highlighted by The Constructor, can significantly enhance the takeoff process, yielding more precise and reliable results.
- Embracing Building Information Modeling (BIM): BIM represents an advanced step in digital takeoffs, utilizing a model-based approach for even greater accuracy. Several software tools leverage BIM to produce precise quantity takeoffs, harnessing detailed visual and specification data from the project for efficient planning.
- Accounting for material cost fluctuations: Construction material costs are subject to frequent changes. An accurate takeoff process must anticipate these fluctuations, estimating costs for the worst-case scenarios to safeguard the project’s budget and timeline.
- Optimizing workflows with cloud-based tools: As project scopes expand, so does the complexity of the takeoff process. Cloud-based solutions optimize workflows, allowing for real-time saving and editing of information. This technology streamlines collaboration, reducing the time lost in meetings and minimizing errors due to miscommunication.
- Implementing a master checklist: Utilizing a comprehensive checklist that covers all standard items required for takeoffs can prevent omissions that lead to project overruns. This checklist should be regularly updated to include any previously missed items, serving as a reliable reference for estimators.
- Integrating with the estimation process: Some takeoff software allows for direct integration with cost estimation processes, enabling swift adjustments for material costs and other estimate components. This integration helps to save valuable time and effort.
These strategies allow construction professionals to refine their takeoff procedures, enhancing the accuracy of project planning while also bolstering the overall management and execution of construction projects.
Summing up the impact of accurate takeoffs on construction success
As we’ve covered construction takeoffs, from their importance in project planning to the differences between manual and digital approaches, it’s clear that the accuracy of takeoffs can lay the cornerstone for project success. Understanding the basic principles of takeoffs and embracing advanced tools like construction takeoff software can significantly mitigate risks, unlock efficiencies, and lead to considerable cost savings that support your project’s bottom line.
The industry’s shift from manual to digital takeoffs underscores a broader trend of embracing technology to meet the constantly evolving demands of construction projects. This transformation from traditional methods to digital solutions is reshaping the way projects are planned, executed, and delivered.
Accurate quantity takeoffs help to optimize resource allocation, improve bid competitiveness, and safeguard against the financial uncertainties that can plague construction projects. The consequences of inaccuracies, especially in heavy construction, emphasize the need for precision in every calculation, every estimate, and every step of the construction process.
In this era of rapid technological advancement and increasingly complex construction projects, arming yourself with the knowledge of best practices in takeoffs, leveraging tools like BIM, and implementing strategies for fluctuating material costs are essential for maintaining a competitive edge in the construction industry.
As part of our commitment to supporting construction professionals, we invite you to experience the cutting-edge capabilities of TCLI’s estimating software. For those looking to see the difference these programs can make, we offer a free 14-day trial, providing an opportunity to explore the features and benefits firsthand. Additionally, for any inquiries or further assistance, feel free to contact us.
Embracing these advanced methods and tools is an investment in your future, ensuring that your projects are managed with the highest degree of efficiency and financial savvy.